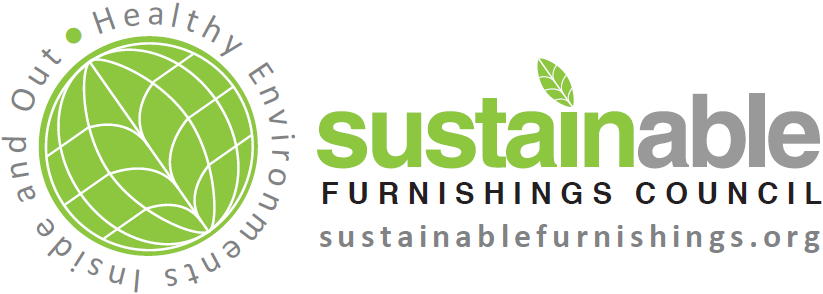
You are here
Huntington House, Inc.
Best Practice Achievements
2019: We keep almost ALL - almost 100% - of our waste out of the landfill. We recycle everything. We've trained our teams to sort each type of manufacturing and packaging waste. We give our sawdust waste to another local furniture company and they use it in their boiler to heat their facility. We re-purpose or donate wood palettes. We can make utility bins or bucks out of palettes or scrap wood for workers to use at their stations.
We have upgraded our method of cutting wood frames, using a CNC machine instead of a person which can "nest" the pattern parts, making more efficient wood cuts with less wood waste. This has reduced our wood waste by 2/3rds. We can reuse some of the wood drops have become other parts of a furniture frame. There are people who operate the CNC machine, so no one loses a job.
We keep our cut frame parts organized into a system, and if a furniture frame is discontinued, we try to reuse those parts to build other frames.
Most of our furniture is built to order, so less storage or floor space is needed to keep inventory.
Our wood finishes have less or no VOC's, though the finishers use respiratory masks to keep from breathing in any fumes.
The factory's air compressor system is programmed to be off when not in use, so that saves money and energy.
We have changed our lighting to LED light fixtures and bulbs. We recycle the bulbs - and even pay to recycle some.
2014: We will initiate an energy audit and seek to reduce our energy consumption
2019: We have become members of Appalachian Hardwood Manufacturers, Inc., which provides certification that the wood we purchase is Verified Sustainable and Verified Legal.
To create our frames, we use glue dowels instead of an adhesive. The glue is activated by steam, and it is water-soluble. This works very well - it creates a secure attachment, its efficient for the operators to use and less messy. We don't have any waste with this type of product - no chance of spills, no harmful VOCs, and no containers to throw away.
The foam we use in our upholstered pieces is CertiPUR certified - made without harmful chemicals, including formaldehyde, and has extremely low VOC emissions.
2018 (and prior): We mainly use hardwood and some plywood that is from a certified source, some of it is FSC Certified.
2014: We seek to improve our efficiency and reduce waste in our woodworking operations
2019: GREEN AP on staff.
We are updating our website to reflect our values in sustainability.
We have a Wellness Plan in place for our employees and staff, with an incentive to create health and wellness in their lives.
Our Human Resource Assistant is becoming a sustainability expert, and is planning to take SFC's GREENleaders course to become more familiar with materials and resources to use (and those to avoid) for the continuous improvement of our manufacturing and for the safety of our workers.
We are educating our Sales Team on the benefits of SFC membership, and on the sustainable efforts we have in place. We see it is a value, a talking point, and a sales strategy to use with our dealers and end users.
2018: We plan to add a sustainability section to our website, educate employees and customers on our sustainability efforts.