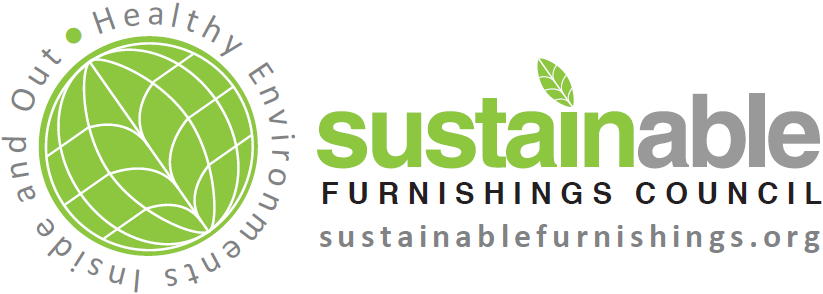
You are here
Gat Creek
Best Practice Achievements
2022: Engineering a high efficiency dust collection system
2020: Same initiatives as 2019.
2019: We continue to monitor energy consumption monthly. We are using less energy per piece we manufacture each year over the last 6 years. We have installed new machinery, making it possible to produce more in-house. We thereby reduce our transportation footprint, which is a priority since in the US transportation has overtaken electricity generation as the leading source of CO2 emissions. We are continuing to reduce transportation emissions in this manner.
2018: Still working on 2017 initiatives.
2017: We plan to install an EcoGate variable drive system to make our dust collection more energy efficient and have explored ways to reduce our reactive power usage.
2016: We installed 64.4 kW of US-made PV solar panels on our south-facing roof that will replace electric we purchase from our coal-burning utility company, First Energy.
2014/2015: We re-lamped the entire factory with LED lighting. This recently completed project will reduce our lighting related electrical use by 70% and our overall electrical use by nearly 25%. We're also replacing a 1950's era planner with a new, more energy efficient planner/sander.
2013: We are updating lighting, replacing older machinery with more efficient new equipment, reducing our component outsourcing via our new machining capabilities, and expending the use of our biomass boiler in our air make-up system to further reduce propane usage.
2012: We are currently evaluating replacing our fossil fuel heating system with one that will use our wood waste--replacing non-renewable fuel with renewable fuel.
2022: Continue local sourcing of all Appalachain Hardwoods.
2020: I serve on the Appalachian Hardwood Manufacturers Inc (AHMI) board of directors and work to better learn our supply chain and assist in it's 100+ year record of sustainability. We're growing trees in the Appalachian Forest 2.4x faster than they are dying and being timbered.
2019: We continue to use all local woods, contributing to the health of our local forests.
2018: We are purchasing a new 5-axis CNC that will use 40%+ less electric than the 15 year-old 3-axis CNC it's replacing.
2017: We are purchasing a new CNC Lathe to bring machining of various parts in-house to reduce transportation of those parts.
2016: We are implementing various projects to continue to our lumber yield improvement in our woodshop and the transfer efficiency in our finishing room.
2014/2015: We are re-organizing our rough-end shop to improve lumber yield.
2013: With our new biomass boiler, we have achieved and maintain zero-waste with our sustainably-sourced lumber and are now focused on our finishing materials. This year we will move 100% water-based paints and are investigating opportunities to reduce formaldehyde used in our catalyzed lacquer and other clear top coats
2012: We will increase the number of products we manufacture that are FSC certified.
2022: Serve as Treasure for SFC
2020: We continue to educate our retail customers about sustainability of solid Appalachian hardwoods and our central location that absolutely minimizes oil-intensive transportation.
2019: We are pleased to sell to several retailers who score Top Tier in the annual Wood Furniture Scorecard assessment.
2018: Same as 2017.
2017: Gat Caperton is serving on the SCF Executive Committee and chairing its Standards Committee.
2016: Distributing new catalogs with more extensive explanation of our sustainability system and results. Also looking for more opportunities to improve the transparency of our manufacturing.
2014/2015: Working with the SFC Standards Committee to better define exemplary standards and help promote the companies that achieve them.
2013: Provide education to customers and suppliers on the benefits of/and awareness to sustainability.